Why is Restoration Equipment Tracking Essential to Your Operation?
Last updated: August 20th, 2024
Contents
Like any contractor in the construction industry, restorers need the right equipment and supplies to do their job. Yet, in the disaster remediation sector, there’s often the need to bring critical assets like dehumidifiers, deodorizers, PPE (personal protective equipment), rescue struts, scrubbers, vacuums, and other gear to locations that need them yesterday. Yet nearly every restorer will have at least one story about their frustration when trying to track down a vital piece of their restoration equipment. Tracking equipment can be extremely challenging, especially when a restoration contractor has multiple ongoing projects.
Often, in the aftermath of a disaster, teams rush from one place to the next to stabilize sites to prevent further damage, and inevitably, they sometimes leave behind gear that’s needed for another structural restoration. Equipment tracking systems these days often utilize RFID (radio frequency identification) tags that can help reduce the chance of this happening. When connected to software, these RFID tags provide a project manager with the exact location of every piece of marked restoration equipment. Tracking essential tools and other equipment helps make a restorer’s job easier, allowing a contractor to do more work while ensuring it’s done more efficiently.
Optimize your restoration projects with Albi’s management software. Schedule a free demo today to see how we can streamline your workflow and enhance your communication with stakeholders.
The Benefits of Restoration Equipment Tracking
Asset management is a problem with many businesses, and it’s no different with contractors who work to remediate damage after a disaster. Tracking these assets is imperative to prevent the loss of valuable restoration equipment. Knowing that the nearest dehumidifier is just down the road saves time and helps prevent further impairment to an already water-damaged structure while having the right PPE for a worksite protects workers. By keeping track of their restoration equipment, restorers can make their operations more efficient, leading to happier customers and higher profits. But these aren’t the only advantages of an equipment tracking system.
Some benefits restoration equipment tracking offers includes:
- Ensuring the right equipment, materials, and tools are available for a project to optimize efficiency.
- Identifying which field team is currently using a certain asset to manage vital pieces of equipment.
- Knowing exactly where valuable pieces of equipment are in real-time.
- Providing a record of the age and condition of specific assets, purchase dates, and serial numbers.
- Recording ongoing upkeep for specific pieces of equipment, reducing downtime due to the need to maintain, repair, or replace them.
Sometimes with restoration equipment, tracking just mitigates forgetfulness. Even the most careful project manager’s memory slips from time to time, especially when dealing with a disaster’s aftereffects and multiple projects. This can in turn lead to the misplacement of an essential piece of restoration equipment. Tracking systems make such oversights easily remedied, while protecting a disaster remediation company’s most valuable assets.
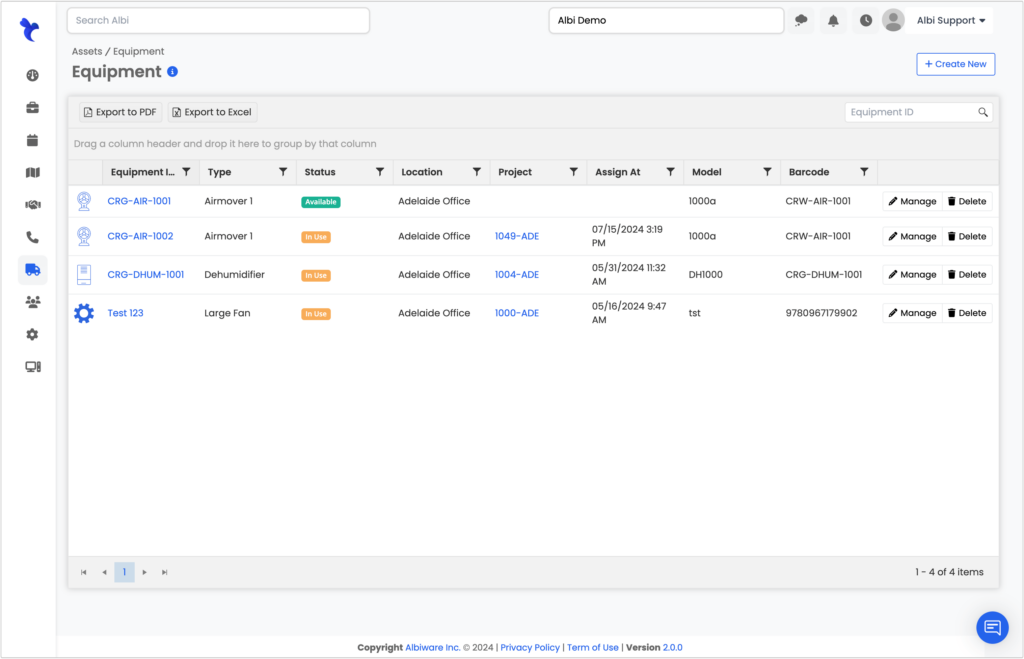
Setting Up an Effective Tracking System for Restoration Equipment
While it’s clear that an effective restoration equipment tracking system can help prevent asset loss and make a contractor’s business run more efficiently, setting up such a system entails more than just purchasing advanced software and other technology. It requires careful planning to understand how best to spend finite business resources to glean the best return on investment (ROI). Inevitably, this will take valuable time out of employees’ days to make an accurate inventory of all a company’s assets, so this should be done during times when there aren’t so many projects on the go.
Steps to follow when setting up a restoration equipment tracking system:
- Determine what requires tracking: This should involve looking at both the most valuable and vulnerable assets a restoration contractor has. This might include easily forgotten pieces of equipment like air movers or PPE for field teams, as well as more expensive items like vehicles.
- Recording assets: Once the items that need to be tracked have been determined, making an accurate inventory of them should be prioritized. This should involve making an account of every piece of equipment by photographing and labeling it while also storing information about each in a centralized system, which ideally will include cloud-based software to track items in real-time from anywhere.
- Tracking asset lifecycles: As part of any restoration equipment tracking system, careful notes should be made on each item’s maintenance and use. This helps determine when an item needs to be maintained, repaired, or replaced, which is useful for budgeting.
- New restoration equipment: Tracking systems should enable a company’s office staff to add new assets to the system quickly. This way, contractors can monitor uptime and downtime of equipment while helping to evaluate maintenance expenses so that an item’s value to the business can be better established over time.
- Marking assets: Regardless of how a company keeps track of restoration equipment, tracking systems should establish a unique means of identifying an item. Whether this is done through an RFID chip, individualized coding or some other means of classification, it helps contractors better differentiate between assets of similar types while aiding planning.
- Asset tracking software: Technology these days is driven by software, which does much more than simply tracking a company’s most expensive hardware. These days, restoration equipment tracking software can be used to track work orders and repairs and order spare parts; it can be used to measure uptime, downtime, and even communications regarding its use.
- Locating restoration equipment: Tracking in real-time offers a restorer many benefits, but one of the most basic features allows contractors to identify exactly where an item is at all times. Unlike a factory or other stationary business, a restoration contractor’s tools and equipment often move from place to place as needed, so having a unique code for each item can save money and time.
- Company needs: Not every restoration equipment tracking system will work for every company. In fact, the actual location of a piece of equipment may be less valuable to certain contractors than tracking whether an item is currently in use, along with the work order to which it’s currently assigned.
- Employee responsibilities: Not only do restoration equipment tracking systems assist with monitoring the tools themselves, they also keep track of who is using them as well. This will take additional training, but will in turn make certain that the equipment, materials, and tools needed for a job are available when and where they’re needed.
When it comes to setting up a system for tracking restoration equipment, training employees to use it correctly may present a challenge. Oftentimes, when a new system is put in place, workers tasked with using it may not understand the relevance of certain features, so it’s important to set clear objectives for everyone who will use it.
Setting Clear Objectives
This is where planning comes in. Regardless of the type of restoration equipment, tracking systems should help contractors achieve clear, companywide goals that help project managers, field teams, office staff and anyone else involved in maintaining inventory. This might involve establishing strategies for sharing certain equipment among teams working in close proximity to each other, or it could involve ensuring that most equipment maintenance is done at times of the year when there’s typically less work. Priorities for tracking restoration equipment should be of the most critical pieces of equipment that are vital to a contractor’s business. Though inventory management should be guided by certain rules, a strategy to track equipment should also be flexible enough to enable improvements or any necessary changes.
Components of an Restoration Equipment Tracking System
Though we’ve touched on steps to develop a strategy for tracking restoration equipment, it’s also important to make sure all a system’s working parts function as they should. Designing a comprehensive tracking system also involves looking at its various components, which include both hardware and software. The various parts of any equipment tracking system should work together to enable effective monitoring of all important assets.
Key components of a restoration equipment tracking system include:
- Labels or tags: Typically in the form of barcodes or RFID tags, these physically identify each asset.
- Scanners or readers: Scanners for barcodes or readers for RFID tags capture data on each marked piece of equipment. Barcode scanners are basically the same as those used in stores that provide prices of items at checkout. RFID readers identify items wirelessly with RFID tags that use radio frequencies. QR codes, a type of barcode, can even be read by smartphones.
- Software: A centralized cloud-based platform is used for viewing details, tracking, scheduling maintenance, generating reports and other tasks related to specific assets, including the storage and management of asset-related data.
Software is critical to any modern equipment tracking system. But it must also have the tools necessary to effectively manage a contractor’s restoration equipment. Tracking software should include a centralized database, have tools to manage check-ins and checkouts, provide a means for identifying each item and have features that support maintenance and repair of each item.
Tips on Training Employees to Use an Restoration Equipment Tracking System
Implementing a system for restoration equipment tracking can be done without technology, and it’s smart to have a fallback strategy should disaster strike those who help others restore damage from disasters. However, this will likely be a very rare occurrence, as these days most inventory management software platforms average at least 99.95 percent uptime, with some of the better cloud-based platforms having an average uptime of 99.99 percent. Sure, a restorer should plan for and have a contingency plan, but since cloud-based platforms will remain up the vast majority of time, it’s important that all employees are sufficiently trained to use it.
Some things to keep in mind when training on a new equipment tracking software platform:
- Engage an employee who can serve as an internal expert about the system and how to use it.
- Ensure all employees can contact the support team for any questions or technical assistance.
- Establish how easy it is to connect physical hardware like tracking tags or barcodes to restoration equipment tracking software.
- Explain the need for tracking restoration equipment and how it will make employees’ jobs easier.
- Inform about how cloud-based equipment tracking solutions enable accessibility from anywhere at any time.
- Provide ample and ongoing training to show how equipment tracking software works.
- Show how automation is more effective than manual methods for managing assets.
- Take advantage of tutorial videos and other training materials that a software-as-a-service (SaaS) provider of equipment tracking platforms might offer to help with its adoption.
Many SaaS companies who provide inventory management platforms for restoration companies require payment for training on top of the monthly fees they charge, with some even requiring a substantial mandatory training fee. Others offer free basic training, while offering advanced training optionally as an additional expense.
Properly Maintaining an Equipment Tracking System
Like any physical infrastructure a contractor might use, restoration equipment tracking software needs to evolve. This may be due to changing technology, new regulations or other factors. To stay reliable and relevant, an equipment tracking system for restoration companies must be continually updated. Though automatic upgrades happen regularly with all cloud-based platforms, data concerning each item being tracked sometimes also needs to be revised occasionally. This includes inputting pertinent details about each item’s condition and maintenance history, along with any other considerations.
Additionally, data should be routinely backed up and preserved in the cloud, which will protect against system failure or physical damage and enable data restoration. Equipment tracking platforms, like any software, also requires robust diagnostics to help with troubleshooting any issues before they affect the system’s functioning. Much of this is done through monitoring by the SaaS provider, though users should always be vigilant about any trouble they might have with the platform.
Above all, a restoration contractor should make sure the vendor with whom they work reacts to feedback to ensure their customers’ needs are met. This includes making sure new capabilities are easily understood and that the system will continue to serve their needs now and into the future. Incorporating an equipment tracking system, Albi is a cloud-based restoration software platform made by and for restorers. To learn more about what Albi can do for you, book a free demo today!
What you should do now
- Get a Free Demo and see how Albiware can help solve your restoration software challenges.
- Read more articles in our blog.
- If you know someone who’d enjoy this article, share it with them via Facebook, Twitter, LinkedIn, or email.